Enterprise Centre, University of East Anglia
The Enterprise Centre is pioneering in its construction techniques, may of which featured a number of ‘world firsts’ for the Construction industry. With dual certification of Passivhaus and BREEAM Outstanding accreditation, this exemplary low carbon building uses an abundance of local natural materials, including Norfolk flint, straw, timber, hemp fabric, re-processed glass, re-purposed mahogany benches, reclaimed oak, clay plaster and nettle boards.
Key Stats
80% natural materials used as part of its construction (thatch, flint, oak, timber)
408 square metres of solar panels
65% lower carbon emissions than a conventionally built Higher Education building
£1.34 LM3 score (for every £1 invested, £1.34 reinvested within 25 miles)
99.41% waste diverted from landfill
26 awards won for its innovative construction methods
At a Glance
Budget
£11.6 million
Completion
2015
Location
Norwich
Sector
Higher Education, Commercial
The centre is part of an ongoing trend in the Higher Education sector that the Morgan Sindall Construction team is proud to be a part of that sees academia joining forces with industry to create hands on experiences for students and for businesses to foster the next generation of innovation and best practice. Similar examples of these projects include the GSK Building for Nottingham Trent University and the Collaborative Teaching Labatory for the University of Birmingham.
Our approach
This collaborative, ground-breaking Passivhaus project was very much a labour of love for all those involved in the project, who were thrilled to deliver something that really showcased genuinely sustainable design.
The team’s commitment to using indigenous materials, coupled with their focus on utilising local suppliers, contractors and craftspeople, gives the building a real sense of identity and enhances its connection to Norfolk. It’s been great to be able to harness these talents, skills, and products and merge them with the most current sustainable technologies and techniques to create this truly remarkable building which will play a valuable role in driving forward innovation in the region.
Take a look at similar Higher Education projects we've delivered
Higher Education (HE)Social impact
A commitment to employing as many local suppliers as possible saw the team engage the Forestry Commission to source local timber from Thetford Forest. They supported local thatchers in the achievement of their CSCS and safety qualifications, meaning they are now able to work industry-wide.
The project also assisted over 300 SMEs with tours and demonstrations, creating more than 200 local jobs. Being considerate to the community, University and surrounding neighbours was important – site team members met monthly with community and University groups ensuring Morgan Sindall Construction’s approach was built around their needs. This helped the project score 45/50 under the Considerate Constructors Scheme.
The Morgan Sindall Construction team was proud to deliver such an innovative building with such exemplary low-carbon emissions. The sub base was 100% recycled and a unique low carbon concrete mix was used in the building foundations. What’s more the building's insulation was produced from 100% recycled newspapers.
The use of local, natural materials has significantly contributed to the reduced emissions from the building. Over it’s proposed 100-year lifespan the building will emit 443kg/Co2/m2, which is about a third of what would normally be emitted from a typical higher education building of this size.
The team also put in a place a post-occupancy evaluation (POE) to review the building every year for a three period after its delivery to ensure the building was still on track to continue to deliver its sustainability goals against the original design. The team was thrilled to find in year one that the building performed better than expected.
You have to bring in a really top team to achieve such an ambitious project. I’m glad to say we achieved what we set out to do, and it’s setting probably the highest standard in Britain and Europe for environmental performance. I think we’ve managed to achieve a great building, and we’ve done it with a great team.
John French, CEO, Adapt Low Carbon Group
Gallery
Related News
NEWS
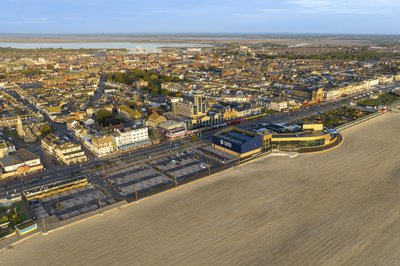
Building Community in Great Yarmouth
The UK's coastal communities face unique challenges. Around 10% of the nation's population lives in coastal towns and cities – places that have experienced decades of decline and where …
NEWS
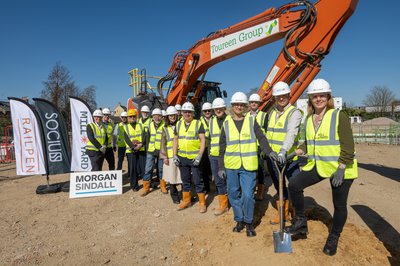
Groundbreaking ceremony marks official start on site for Mill Yard development
A major milestone was reached on Monday 7 April as local councillors, residents, members of the community and the development project team all attended an official groundbreaking ceremony for …
NEWS
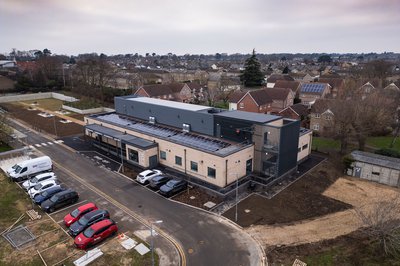
Morgan Sindall completes Newmarket Community Diagnostic Centre
A new Community Diagnostic Centre (CDC) at the Newmarket Community Hospital has been completed by Morgan Sindall Construction and handed over to West Suffolk NHS Foundation Trust (WSFT).