Cosham Fire Station
Delivered through the SCF framework, Cosham Fire Station is the final piece of the puzzle for the Hampshire & Isle of Wight Fire & Rescue’ (HIWFRS) estate. Completing a trio of fire stations and delivered by the Morgan Sindall Construction’s Southern team, Cosham Fire Station is a new three storey facility providing staff welfare and community facilities, a police station and training tower.
Key Stats
- Delivered on time and budget
- 445 training weeks provided to students
- 16 Engagement events carried out during the project
- 556T of Carbon saved throughout construction of the new facility
- 10/10 customer satisfaction
At a Glance
Budget
£16.5m
Completion
July 2024
Location
Portsmouth
Framework
Southern Construction Framework (SCF)
Sector
Emergency Services, Fire
The recent history and purpose of the project
Formerly located on Wayte Street in Cosham, it was decided that the Cosham Fire Station would be demolished and relocated onto the site of the former Portsmouth Craft and Manufacturing Industries (PCMI) on Northern Road. Following approval from the Fire Authority, the aspiration for the project was to provide improved working and training facilities for firefighters in the area, along with facilities for community uses. Increasing space was also key, with the new fire station spanning across two acres of land and rising three stories high.
The new fire station, which acts as a training hub for the southern region, incorporates a new training tower along with additional training facilities for operatives. As improved training was a fundamental requirement for the project, the tower has been designed in such a way, that both the exit and entrance could be adapted; providing trainees a challenge every time they enter the building.
A specialist decontamination design
The operatives who work within these buildings are exposed to heavy amounts of fire and smoke which carry several toxins, meaning operatives are often left contaminated. As such, the building had been designed to have a decontamination route so that operatives now follow a decontamination process as they journey through the building. The decontamination route is colour coded as:
- Red - Removal of contaminated clothing
- Amber - Shower and clean for removal of smoke on skin etc
- Green - Decontaminated area such as admin wing and appliance bay
This process reduces the associated risks to operatives health and protects the operatives from the harmful toxins that they would ordinarily have to deal with daily.
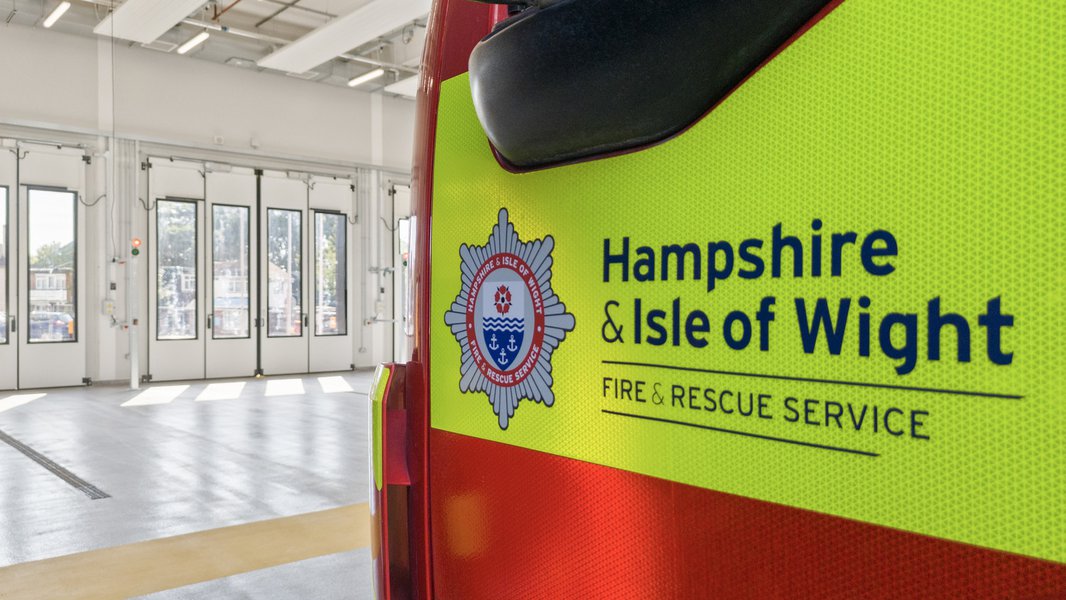
Meeting the logistics challenge
During the construction of the fire station, one of the biggest challenges the team faced was the location of the project. The project was located on a busy five lane intersection, whereby three of the lanes’ head towards a large roundabout and the other two lanes take you away from the roundabout. Due to this, it was important for the project team to devise a robust traffic management strategy to mitigate as much disruption as possible in this area.
Initially there was only one access onto site via an entrance on Northern Road opposite 'Northern Dental'. Upon the site, there was an existing building which was originally due to be demolished. A care home was meant to be constructed, which meant the site entrance on Northern Road would be the only possible entry/exit point onto site. However, by identifying the care home was no longer in the pipeline, it meant it was possible to build a new entrance/exit onto site behind the development. As a result, this acted as a two way exit and entry onto site, removing the possible challenges on the key city roundabout.
Saving over 556T of carbon
From start to finish, the project team worked collaboratively with all stakeholders on the project to innovate ways to reduce the carbon impact of the project. The project team participated in the 10 Tonne Challenge and were able to reduce a combined total of 556T of carbon. This was achieved by:
- Changing the foundation of the building from concrete piling to pads, which resulted in significantly reducing the amount of material required
- Opting for HVO fuel as an alternative to diesel, making it a diesel free site
- Inclusion of Air Source Heat Pumps
- Over 219 PV panels
Social Value Impact
The team donated roughly £3,000 towards the purchase of new equipment for the Queen Alexandra (QA) Hospital Portsmouth. The donation has gone a long way to support the staff on the Paediatric Starfish Ward. As a busy hospital covering a large and diverse area, QA Hospital have been seeing a growing number of children using their services who need high dependency care. To help continue providing great care to these children, they needed some new equipment to support nursing staff to stay closer to the child when they need increased observations or one-on-one nursing. Our donation towards purchasing new nursing trolleys, stools, fluid stands for children having multiple infusions, and brightly coloured tables has really helped improve the experience of patients.
Months later, the project team including Hampshire Isle of Wight Fire Rescue Service came back to visit the hospital, to see the equipment being used first hand.
"We are excited to use our new equipment and have already had so much positive feedback from families, children, and our staff. Thank you so much.”
Charlotte Misselbrook, Paediatric Nurse, Starfish Ward
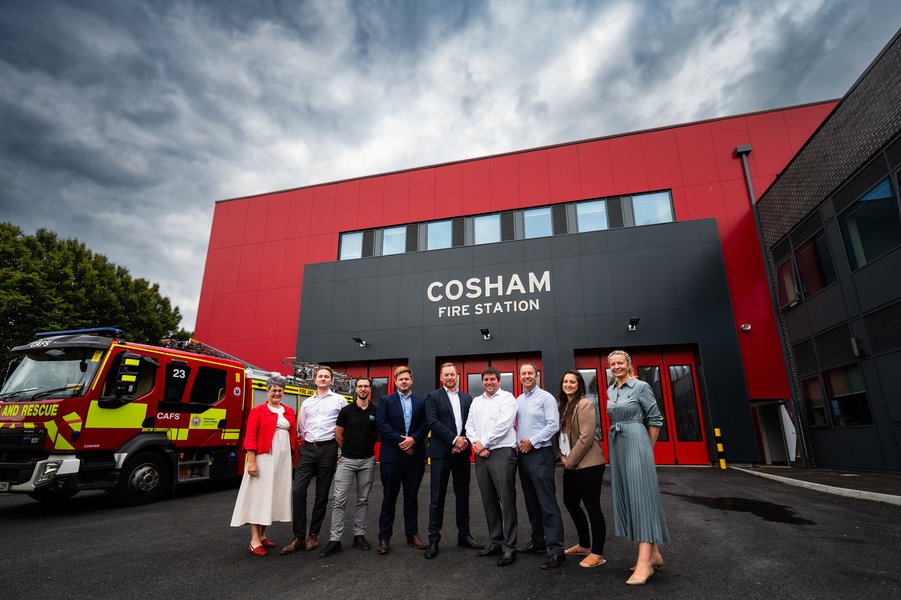
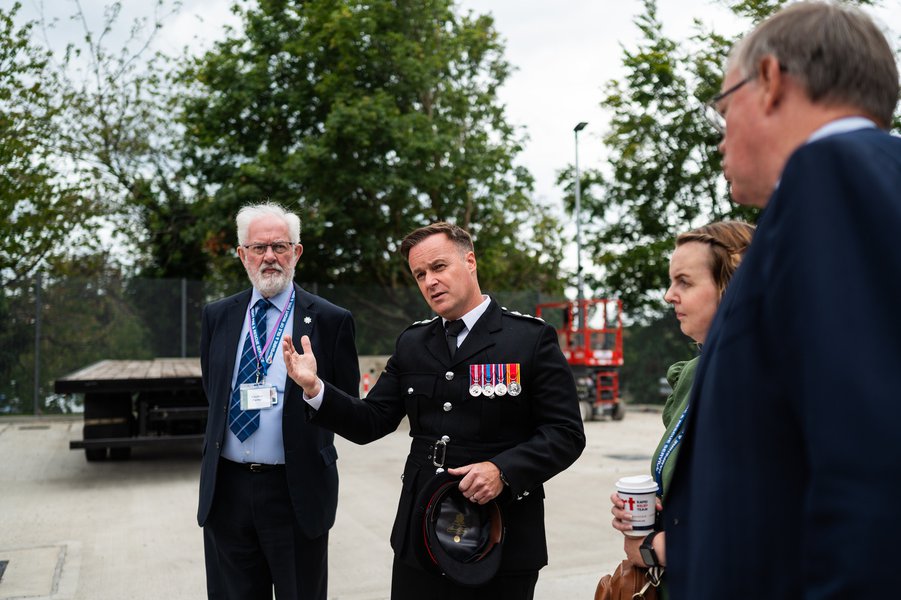
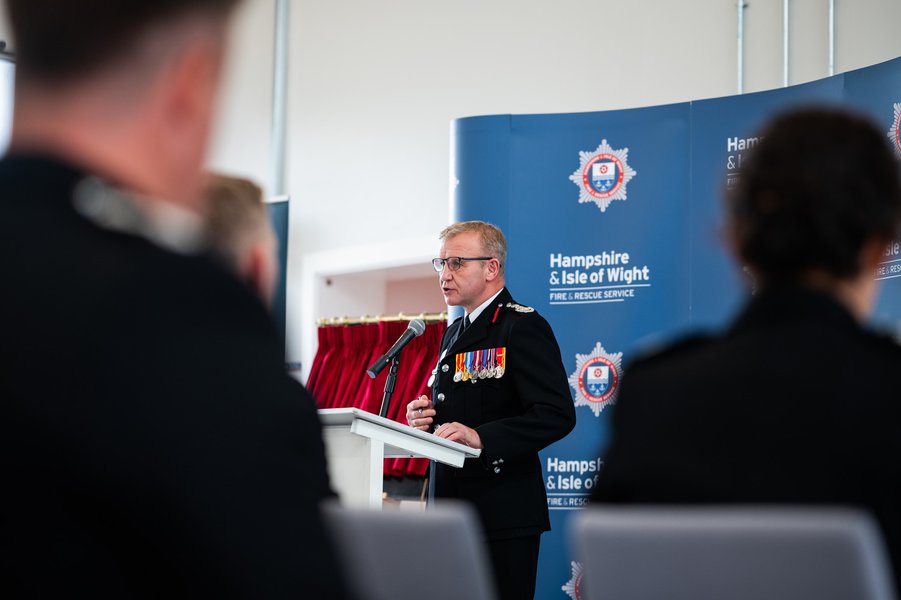
The staff here are blown away. I think it’s hard not to be impressed and it’s hard not to be grateful for the facilities. It’s incredibly airy, there’s so much space but it doesn’t feel clinical – it still feels like home and strill feels like a fire station should. It’s an amazing place to come and work.”
Lee Sheen, Fire Station Commander
Gallery
Related News
NEWS
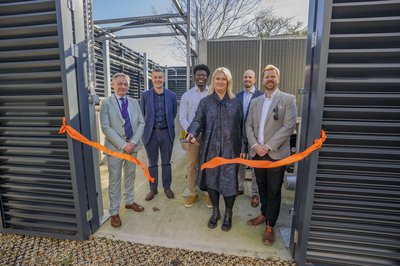
Morgan Sindall Construction and Arts University Bournemouth celebrates completion of decarbonisation project
On Thursday 20 March, Morgan Sindall Construction and Arts University Bournemouth (AUB) celebrated the completion of a decarbonisation project which saw the installation of Air Source Heat Pumps (ASHPs) …
NEWS
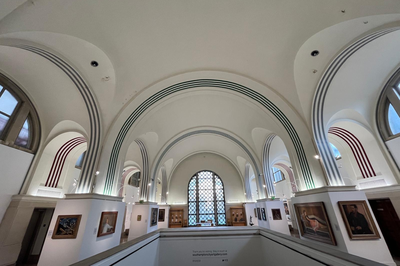
Morgan Sindall Construction leads next phase of Southampton City Art Gallery’s historic renewal
Morgan Sindall Construction has commenced the next phase of a £4.3m restoration project at the Grade II* listed Southampton City Art Gallery, marking a significant milestone in the preservation …
NEWS
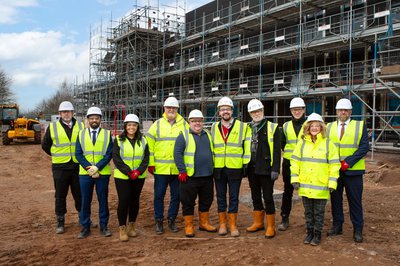
Morgan Sindall celebrates structural milestone at Nottinghamshire SEN school
Morgan Sindall Construction has marked a major milestone in the delivery of Horizons Academy, a new state-of-the-art, specialist educational needs (SEN) school in Mansfield, with a structure signing event.